電鍍廢氣處理設備塑性加工工序:工藝、技術與
未知, 2025-06-21 14:16, 次瀏覽
電鍍廢氣處理設備塑性加工工序:工藝、技術與質量控制
在現代工業生產中,電鍍行業作為重要的表面處理工藝,廣泛應用于汽車、電子、機械等多個***域。然而,電鍍過程中產生的廢氣不僅對環境造成污染,還可能危害人體健康。因此,電鍍廢氣處理設備的制造顯得尤為重要,而其中的塑性加工工序更是關鍵環節之一。本文將詳細探討電鍍廢氣處理設備塑性加工工序的各個方面,包括工藝流程、技術要點、質量控制以及未來發展趨勢。
一、電鍍廢氣處理設備概述
1.1 電鍍廢氣的來源與成分
電鍍過程中,由于電解作用,會產生***量含有重金屬離子(如鉻、鎳、銅、鋅等)和酸性氣體(如硫酸霧、硝酸霧)的廢氣。這些廢氣若未經處理直接排放,將對***氣環境造成嚴重污染,甚至通過食物鏈積累影響人類健康。
1.2 電鍍廢氣處理設備的分類
根據處理原理的不同,電鍍廢氣處理設備主要分為以下幾類:
物理法:如吸附法、冷凝法等,通過物理手段去除廢氣中的有害物質。
化學法:如吸收法、催化燃燒法等,利用化學反應將有害物質轉化為無害物質。
生物法:利用微生物的代謝作用降解廢氣中的有機物。
其中,吸收法因其高效、經濟的***點,在電鍍廢氣處理中應用***為廣泛。
二、塑性加工工序在電鍍廢氣處理設備制造中的重要性
塑性加工是電鍍廢氣處理設備制造過程中的關鍵步驟,它涉及到設備的結構強度、密封性能、耐腐蝕性等多個方面。***質的塑性加工能夠確保設備在惡劣的工作環境下長期穩定運行,提高處理效率,延長使用壽命。
三、電鍍廢氣處理設備塑性加工工序詳解
3.1 材料選擇與預處理
3.1.1 材料選擇
電鍍廢氣處理設備通常選用耐腐蝕、高強度的塑料材料,如聚丙烯(PP)、聚氯乙烯(PVC)、玻璃鋼(FRP)等。這些材料具有******的化學穩定性和機械性能,能夠抵抗廢氣中的腐蝕成分。
3.1.2 材料預處理
在塑性加工前,需對原材料進行預處理,包括干燥、混合、造粒等步驟。干燥是為了去除材料中的水分,防止加工過程中產生氣泡或裂紋;混合則是為了確保材料的均勻性;造粒則是將原材料加工成適合塑性加工的顆粒狀。
3.2 成型工藝
3.2.1 注塑成型
注塑成型是電鍍廢氣處理設備塑性加工中***常用的方法之一。該工藝通過將預熱的塑料顆粒注入模具中,經冷卻固化后得到所需形狀的零件。注塑成型具有生產效率高、制品尺寸準確、表面質量***等***點。
模具設計:模具是注塑成型的核心,其設計直接影響到制品的質量和生產效率。模具設計需考慮制品的形狀、尺寸、壁厚、脫模方式等因素。
工藝參數:注塑成型的工藝參數包括溫度、壓力、時間等。合理的工藝參數設置能夠確保制品的質量穩定。
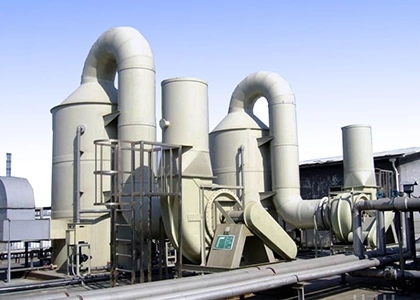
3.2.2 擠出成型
擠出成型適用于生產連續長度的塑料型材,如管道、板材等。在電鍍廢氣處理設備中,擠出成型常用于制造廢氣處理系統的連接管道和支撐結構。
口模設計:口模是擠出成型的關鍵部件,其設計決定了型材的截面形狀和尺寸精度。
牽引與切割:擠出后的型材需經過牽引和切割,以獲得規定的長度和整齊的端面。
3.2.3 吹塑成型
吹塑成型主要用于生產中空制品,如儲罐、容器等。在電鍍廢氣處理設備中,吹塑成型可用于制造廢氣吸收塔的外殼和內部構件。
型坯制備:通過擠出機頭將塑料熔體制成管狀型坯。
吹脹與冷卻:將型坯置于模具中,通入壓縮空氣使其膨脹貼合模壁,經冷卻定型后得到制品。
3.3 后處理與裝配
3.3.1 后處理
塑性加工后的制品需進行后處理,以提高其性能和外觀質量。常見的后處理方法包括退火處理、表面處理、切割和打磨等。
退火處理:通過加熱和冷卻的方式消除制品內部的應力,提高其尺寸穩定性和機械性能。
表面處理:如噴砂、拋光等,可改善制品的表面質量,增強其耐腐蝕性和美觀度。
3.3.2 裝配
裝配是將塑性加工***的零件組合成完整的電鍍廢氣處理設備的過程。裝配過程中需注意零件之間的配合精度和密封性能,確保設備的整體性能和安全性。
密封技術:采用高質量的密封材料和先進的密封技術,確保設備在運行過程中不會發生泄漏。
連接方式:根據設備的結構和使用要求,選擇合適的連接方式,如焊接、螺栓連接等。
四、質量控制與檢測
4.1 質量控制體系
建立完善的質量控制體系是確保電鍍廢氣處理設備塑性加工質量的關鍵。該體系應涵蓋原材料檢驗、過程控制、成品檢驗等各個環節。
原材料檢驗:對進廠的原材料進行嚴格的質量檢驗,確保其符合設計要求。
過程控制:在塑性加工過程中,對每一道工序進行實時監控和記錄,及時發現并解決問題。
成品檢驗:對加工完成的制品進行全面的質量檢驗,包括外觀檢查、尺寸測量、性能測試等。
4.2 檢測技術與方法
為了確保電鍍廢氣處理設備的質量和性能,需采用先進的檢測技術和方法對其進行全面檢測。
外觀檢查:通過目視或放***鏡觀察制品的表面質量,如是否有裂紋、氣泡、飛邊等缺陷。
尺寸測量:使用卡尺、千分尺等測量工具對制品的尺寸進行***測量,確保其符合設計要求。
性能測試:對制品進行耐腐蝕性、強度、密封性等性能測試,以評估其在實際使用中的表現。
五、案例分析:某電鍍廢氣處理設備塑性加工實例
為了更***地理解電鍍廢氣處理設備塑性加工工序的實際應用,以下將以某型號電鍍廢氣處理設備為例,詳細介紹其塑性加工過程。
5.1 設備概述
該電鍍廢氣處理設備采用吸收法處理廢氣,主要由廢氣收集系統、吸收塔、循環泵、風機等部分組成。其中,吸收塔和連接管道是設備的主要塑料構件,采用聚丙烯(PP)材料制造。
5.2 塑性加工過程
5.2.1 材料準備
選用***質聚丙烯(PP)顆粒作為原材料,經過干燥、混合、造粒等預處理步驟后,得到適合注塑成型的顆粒狀物料。
5.2.2 注塑成型
模具設計:根據吸收塔和連接管道的設計圖紙,設計制作相應的注塑模具。模具采用高精度加工中心加工,確保模具的尺寸精度和表面質量。
注塑成型:將預處理***的PP顆粒加入注塑機中,設置合適的溫度、壓力和時間參數,進行注塑成型。成型過程中需密切關注制品的填充情況和冷卻效果,避免出現缺料、縮痕等缺陷。
5.2.3 后處理與裝配
退火處理:對注塑成型后的制品進行退火處理,以消除內部應力,提高尺寸穩定性。
表面處理:對制品進行噴砂處理,以改善其表面質量,增強耐腐蝕性。
裝配:將吸收塔、連接管道等零件按照設計要求進行裝配,采用高質量的密封材料和先進的密封技術,確保設備的密封性能。同時,對裝配***的設備進行全面的性能測試,包括氣密性測試、吸收效率測試等,以確保其滿足設計要求和使用需求。
六、未來發展趨勢與挑戰
6.1 未來發展趨勢
隨著環保法規的日益嚴格和工業生產的不斷發展,電鍍廢氣處理設備的市場需求將持續增長。未來,電鍍廢氣處理設備塑性加工工序將朝著以下幾個方向發展:
材料創新:研發更高性能的塑料材料,如耐高溫、耐強腐蝕的新型塑料,以滿足更嚴苛的使用環境。
工藝***化:通過引入先進的塑性加工技術和設備,提高生產效率和產品質量,降低生產成本。
智能化制造:利用物聯網、***數據等先進技術,實現塑性加工過程的智能化控制和管理,提高生產過程的可控性和穩定性。
6.2 面臨的挑戰
盡管電鍍廢氣處理設備塑性加工工序取得了顯著進展,但仍面臨一些挑戰:
材料成本:高性能塑料材料的成本較高,增加了設備的制造成本。如何在保證性能的前提下降低成本是亟待解決的問題。
技術門檻:先進的塑性加工技術和設備需要專業的技術人員進行操作和維護,對企業的技術實力提出了更高要求。
環保要求:隨著環保法規的日益嚴格,電鍍廢氣處理設備的環保性能將成為市場競爭的重要因素。企業需要不斷提升產品的環保性能以滿足市場需求。
結論
電鍍廢氣處理設備塑性加工工序是確保設備質量和性能的關鍵環節。通過對材料選擇、成型工藝、后處理與裝配等方面的嚴格控制和管理,可以制造出高質量、高效率的電鍍廢氣處理設備。未來,隨著材料科學的進步和制造技術的不斷創新,電鍍廢氣處理設備塑性加工工序將迎來更加廣闊的發展前景。同時,企業也需要不斷應對材料成本、技術門檻和環保要求等挑戰,以保持市場競爭力并推動行業的可持續發展。