電鍍廢氣處理設備生產合格檢驗方法
未知, 2025-06-21 14:10, 次瀏覽
電鍍廢氣處理設備生產合格檢驗方法
摘要: 本文詳細闡述了電鍍廢氣處理設備在生產過程中的合格檢驗方法,包括外觀檢驗、材料檢驗、結構尺寸檢驗、性能檢驗、電氣安全檢驗以及包裝檢驗等多個方面,旨在確保設備質量符合相關標準和生產要求,為電鍍廢氣的有效處理提供可靠保障。
一、引言
電鍍行業在工業生產中廣泛應用,但其生產過程會產生***量含有有害物質的廢氣,若未經有效處理直接排放,將對環境和人體健康造成嚴重危害。電鍍廢氣處理設備作為防治污染的關鍵設施,其質量合格與否直接關系到廢氣處理效果和環境安全。因此,在設備生產過程中,嚴格的合格檢驗至關重要。
二、外觀檢驗
1. 表面質量
設備表面應平整光滑,無明顯的凹痕、劃傷、銹蝕、變形等缺陷。采用目視檢查和手感觸摸相結合的方式,對設備外殼、管道、部件表面進行全面檢查。例如,對于設備外殼的不銹鋼部分,應無劃痕、銹斑,光澤均勻;對于噴漆部件,應無流掛、起泡、剝落等現象。
檢查設備的涂層質量,涂層應牢固附著在設備表面,不得有脫落、龜裂等情況。可以通過輕輕刮擦或敲擊涂層邊緣,觀察是否有松動或脫落跡象。
2. 標識與銘牌
設備上應有清晰、準確、完整的標識和銘牌。標識應包括設備名稱、型號、規格、生產廠家、生產日期、出廠編號等信息。銘牌應符合相關標準規定,采用耐腐蝕、不易磨損的材料制作,安裝位置應醒目且便于查看。檢查標識和銘牌的內容是否準確無誤,字體是否清晰可辨,固定是否牢固。
3. 焊接與連接部位
仔細檢查設備的焊接部位,焊縫應均勻、連續,無氣孔、夾渣、裂紋等缺陷。對于重要部位的焊縫,可采用無損檢測方法(如超聲波探傷、射線探傷等)進行抽檢,確保焊接質量符合相關標準要求。
檢查設備各部件之間的連接部位,如螺栓連接、法蘭連接等。螺栓應擰緊牢固,無松動、缺失現象;法蘭連接應密封******,墊片安裝正確,無泄漏隱患。可以通過手動擰動螺栓、檢查法蘭間隙等方式進行初步判斷,必要時進行壓力試驗或泄漏檢測。
三、材料檢驗
1. 原材料材質證明
要求設備生產廠家提供主要原材料(如鋼材、塑料、橡膠、金屬材料等)的材質證明文件,包括材料的成分分析、力學性能測試報告、質量保證書等。核對材質證明文件中的材料規格、型號、化學成分、力學性能指標等是否與設備設計要求相符。例如,對于用于制作廢氣處理設備主體的鋼材,應檢查其屈服強度、抗拉強度、伸長率等力學性能指標是否滿足設計工況下的壓力和負荷要求。
2. 材料抽樣檢測
從生產設備所用的原材料中抽取一定數量的樣品進行復檢。對于金屬材料,可以進行光譜分析、硬度測試、金相分析等檢驗項目,以確定材料的化學成分、組織結構和力學性能是否符合要求。對于非金屬材料,如塑料板材、橡膠制品等,可以進行密度測試、拉伸強度測試、耐酸堿腐蝕性測試等。例如,對用于制作廢氣管道的塑料板材,檢測其在不同濃度酸堿溶液中的耐腐蝕性,確保其在電鍍廢氣環境下能夠長期穩定使用。
3. 材料兼容性檢驗
考慮設備在運行過程中各材料之間的接觸情況,檢驗材料的兼容性。例如,檢查廢氣處理設備內部的金屬部件與化學藥劑(如吸收液、催化劑等)之間是否會發生化學反應,導致部件腐蝕或藥劑失效。可以將金屬試樣浸泡在模擬廢氣處理環境的化學藥劑溶液中,經過一定時間后取出,觀察試樣表面是否有腐蝕、變色等現象,并分析溶液中是否有金屬離子析出,以評估材料的兼容性。
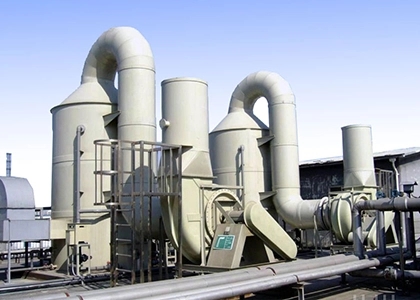
四、結構尺寸檢驗
1. 整體尺寸
使用量具(如鋼尺、卷尺、卡尺等)對設備的整體尺寸進行測量,包括設備的長、寬、高、直徑等關鍵尺寸。將測量結果與設備設計圖紙進行對比,偏差應在允許范圍內。例如,對于廢氣處理設備的塔體部分,其直徑偏差應控制在±[X]毫米以內,高度偏差應不超過±[Y]毫米,以確保設備能夠準確安裝在預定位置,并與周邊的管道、電氣系統等順利連接。
2. 內部結構尺寸
檢查設備內部的關鍵結構尺寸,如廢氣處理腔室的尺寸、填料層的高度和厚度、噴淋系統的噴頭布局和間距等。這些內部結構尺寸直接影響廢氣處理效果和設備的運行性能。例如,填料層的厚度應符合設計要求,以保證廢氣與填料有足夠的接觸時間和面積,提高處理效率。通過實際測量和與設計圖紙的核對,確保內部結構尺寸準確無誤。
3. 裝配尺寸
對于由多個部件組裝而成的設備,檢查各部件之間的裝配尺寸。例如,檢查風機與電機的同軸度、皮帶輪的平行度和張力,確保風機運轉平穩,傳動效率高效。檢查管道連接處的法蘭面之間的平行度和間距,保證管道連接緊密,無泄漏風險。可以使用激光測距儀、水平儀、百分表等精密測量工具進行裝配尺寸的測量和調整。
五、性能檢驗
1. 廢氣處理效率測試
在設備生產線上或模擬實際運行條件下,對電鍍廢氣處理設備進行廢氣處理效率測試。通入模擬電鍍廢氣(成分和濃度與實際廢氣相似),在設備的進口和出口分別設置采樣點,采集廢氣樣本。采用適當的分析方法(如化學吸收法、儀器分析法等)測定廢氣中污染物(如鉻酸霧、硫酸霧、氮氧化物、氰化物等)的濃度。
計算廢氣處理效率,處理效率 =(進口污染物濃度 出口污染物濃度)/ 進口污染物濃度×100%。根據不同的廢氣成分和處理工藝要求,設定相應的處理效率合格標準。例如,對于鉻酸霧的處理效率應不低于[X]%,硫酸霧的處理效率應不低于[Y]%等。若處理效率未達到標準要求,需對設備進行調整或查找原因進行改進。
2. 風量測試
使用風速儀或風量測試儀測量設備的空氣流量(風量)。在設備的進風口和出風口選擇合適的測量截面,按照規范的測量方法(如等面積布點法)測量風速,并根據風速和截面積計算風量。將測量得到的風量與設備設計風量進行對比,偏差應在允許范圍內。例如,設計風量為[Q]立方米/小時的設備,實際測量風量應在([Q] [ΔQ])至([Q] + [ΔQ])立方米/小時之間,其中[ΔQ]為允許的風量偏差值。風量不足或過***都可能影響廢氣處理效果和設備的正常運行。
3. 壓力損失測試
測量廢氣通過設備時的壓力損失。在設備的進出口管道上安裝壓力傳感器或壓力表,通入一定風量的廢氣,讀取進出口的壓力差值,即為設備的壓力損失。壓力損失過***會增加風機的能耗,降低設備的運行經濟性。一般來說,設備的壓力損失應控制在設計允許范圍內,例如不超過[P]帕斯卡。若壓力損失超出標準,需檢查設備的內部結構(如填料層堵塞、管道彎曲半徑過小等)是否存在問題,并進行相應的清理或調整。
4. 噪聲測試
在設備正常運行狀態下,使用噪聲測試儀在設備周圍不同位置(如距離設備表面[X]米處)測量設備的噪聲值。設備的噪聲應符合***家相關標準和環保要求,一般不得超過[N]分貝。若噪聲超標,需檢查設備的風機、電機、傳動部件等是否存在異常振動或摩擦,采取減振、降噪措施(如安裝消聲器、減振墊等)進行處理。
六、電氣安全檢驗
1. ***緣電阻測試
使用***緣電阻測試儀對設備的電氣系統進行***緣電阻測試。測試前,應斷開設備的電源,并將電氣系統中的所有電子元件(如電容器、半導體器件等)進行短接放電處理。然后將***緣電阻測試儀的兩端分別連接設備的電氣回路與外殼接地端,施加規定的直流電壓(一般為 500V 或 1000V),測量***緣電阻值。
根據設備的電壓等級和工作環境條件,***緣電阻應符合相應的標準要求。例如,對于一般低壓電氣設備,***緣電阻不應低于[R]兆歐姆。若***緣電阻值過低,可能存在電氣漏電隱患,需檢查電氣線路的***緣情況,查找***緣破損點并進行修復或更換***緣材料。
2. 接地電阻測試
測試設備的接地電阻,以確保設備在發生漏電故障時能夠有效地將電流導入***地,保障操作人員的安全。使用接地電阻測試儀,將測試電極按照規定的間距插入設備附近的土壤中,然后連接設備的接地端子與測試儀。啟動測試儀,測量接地電阻值。
接地電阻應滿足***家相關標準和安全要求,一般不超過[S]歐姆。若接地電阻過***,需檢查接地裝置(如接地極、接地網)的埋設深度、土壤電阻率、連接情況等因素,采取增加接地極數量、改善接地土壤條件、修復接地連接等措施降低接地電阻。
3. 電氣保護裝置測試
檢查設備上的各類電氣保護裝置(如熔斷器、熱繼電器、過流保護器、漏電保護器等)是否正常工作。通過模擬過載、短路、漏電等故障情況,觀察保護裝置是否能及時動作,切斷電源,起到保護設備和人員安全的作用。例如,在電機負載端逐漸增加負載電流,檢查熱繼電器是否能在設定的過載電流值時及時跳閘;按下漏電保護器的測試按鈕,檢查漏電保護功能是否正常。對于不符合要求的電氣保護裝置,應及時更換或調整。
七、包裝檢驗
1. 包裝完整性
檢查設備的包裝是否完整,有無破損、變形、受潮等情況。包裝箱應牢固可靠,能夠有效保護設備在運輸和儲存過程中不受損壞。查看包裝箱的封口是否嚴密,膠帶是否有松動、脫落現象;檢查包裝箱的四周和***部是否有碰撞痕跡或損壞。對于采用木箱包裝的設備,還應檢查木材是否有腐朽、蟲蛀等問題。
2. 包裝標識
包裝上應有清晰的標識,包括設備名稱、型號、規格、數量、重量、體積、生產日期、生產廠家、收貨地址等信息。標識應符合運輸和倉儲的要求,便于識別和搬運。此外,對于有***殊運輸要求(如防潮、防震、防曬、向上標識等)的設備,包裝上應有相應的警示標志和說明。檢查標識的內容是否準確完整,字體是否清晰醒目,粘貼或印刷是否牢固。
3. 包裝材料與防護措施
檢查包裝材料是否符合要求,如包裝箱的材質、厚度應能滿足設備的防護需求;內部緩沖材料(如泡沫塑料、氣泡墊、海綿等)應足夠厚實、密實,能夠有效減輕設備在運輸過程中的震動和沖擊。對于精密部件或易損部件,應有額外的防護包裝(如單***包裝、加厚緩沖材料等)。同時,檢查設備在包裝內的固定情況,應采用合適的固定裝置(如繩索、卡扣、支撐架等)將設備牢固地固定在包裝箱內,防止在運輸過程中發生位移或晃動。
八、結論
電鍍廢氣處理設備的生產合格檢驗是一個全面、系統的過程,涉及外觀、材料、結構尺寸、性能、電氣安全以及包裝等多個方面的檢驗項目。通過嚴格遵循上述檢驗方法,對每一臺設備進行細致的檢驗,能夠確保設備質量符合相關標準和生產要求,保證其在電鍍廢氣處理過程中穩定、高效地運行,有效減少廢氣污染物排放,保護環境和人體健康。在檢驗過程中,應做***詳細的檢驗記錄,對于不合格項目應及時整改并重新檢驗,直至設備完全合格方可出廠投入使用。